Boeing’s outsourcing strategy under fire after mid-air incident
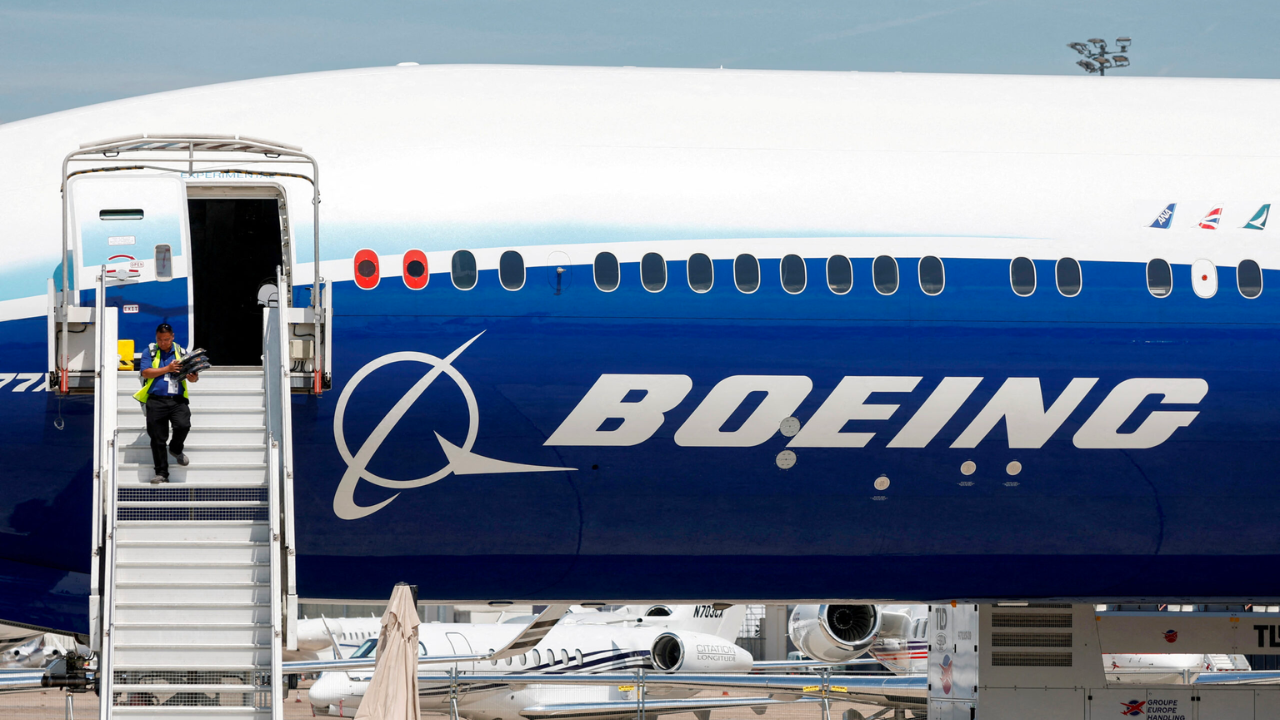
VIRGINIA, UNITED STATES — Boeing’s two-decade-long outsourcing strategy is under intense scrutiny following a series of quality control issues, including a recent incident where a mid-exit door of the 737 Max 9 blew off at 16,000 feet during a flight.
Historically, Boeing maintained a vertically integrated model, but in the early 2000s, the company shifted gears, outsourcing a significant portion of the 787 Dreamliner’s development.
This move, aimed at cutting costs and speeding up production, led to a sprawling, complex supply chain that Boeing struggled to manage.
The outsourcing approach, which saw over 70% of the 787’s design and manufacturing handed off to over 50 key suppliers, has been linked to a range of problems, from production delays to fatal crashes.
The recent emergency landing incident, attributed to missing bolts, has cast a harsh light on Boeing’s oversight and quality control, particularly with suppliers like Spirit AeroSystems.
UCLA Anderson School of Management Professor Dr. Christopher Tang points out that Boeing’s current crisis echoes past issues that arose during the 787 Dreamliner’s development.
He suggests that without significant sanctions and a reevaluation of Boeing’s design and production processes, the company is likely to face ongoing challenges.
Boeing’s reliance on external partners for critical aspects of aircraft production has been questioned, especially in light of Airbus’s better safety record despite a similar outsourcing model.
The situation underscores the importance of robust supplier relationships and quality control systems, which Boeing appears to have neglected in its pursuit of cost savings and efficiency.
As Boeing grapples with the fallout from its outsourcing decisions, the company may need to reconsider its strategy and reinvest in internal capabilities to ensure product quality and safety.