Former Amazon exec optimistic about robots replacing humans
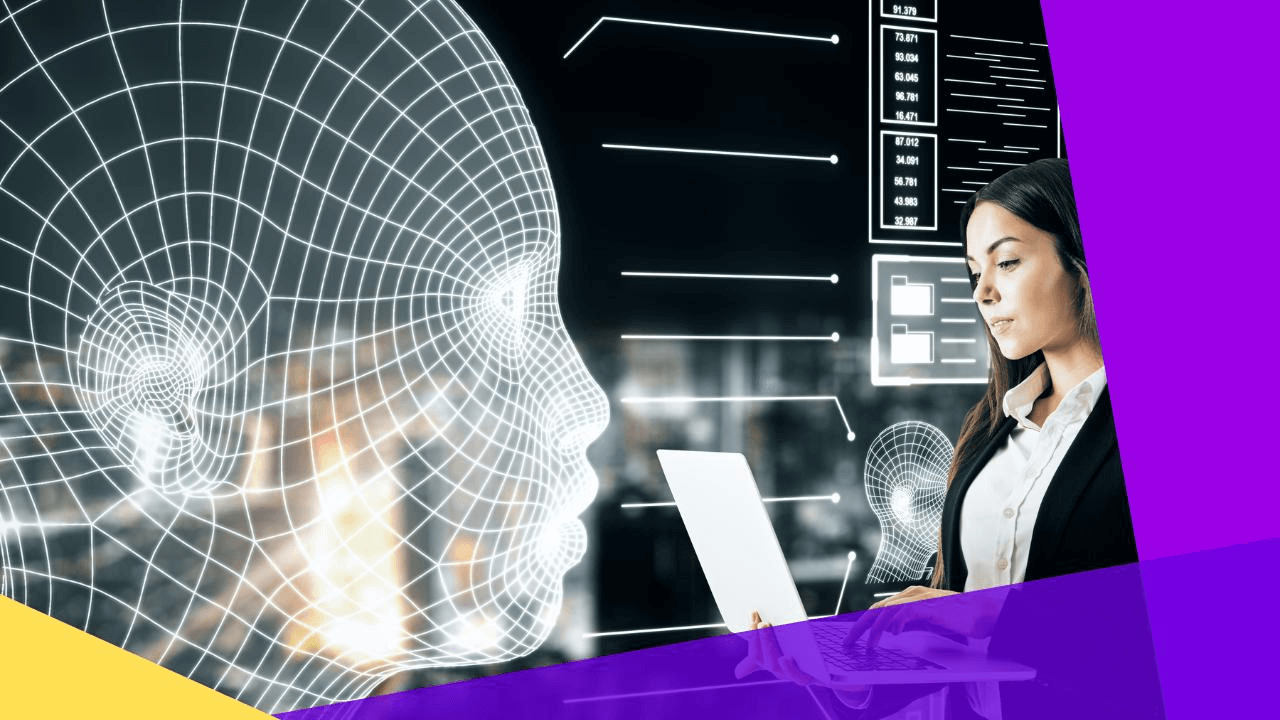
CALIFORNIA, UNITED STATES — The integration of robotics and AI into the workforce is poised to transform traditional labor roles, but this transition may bring more opportunities than concerns.
Dave Clark, former CEO of Amazon’s consumer business, emphasizes that productivity improvements through robotics should be viewed positively, as they enable workers to focus on more intellectually engaging tasks.
“Robotics will drive a ton in labor savings over time,” Clark, now founder of the AI supply-chain start-up Auger, said during Fortune’s Brainstorm AI conference in San Francisco.
“Unfortunately, we’ve made productivity sort of a dirty word. But we keep finding better ways to engage people’s brains.”
AI and robotics transform global workforce
Sanjay Radhakrishnan, CTO of Sam’s Club, joined the panel and discussed how robotic tools have already transformed retail operations. At Sam’s Club, robotic tools have already eliminated approximately 100 million manual tasks previously performed by store employees.
Additionally, Figure’s AI-powered humanoid robot has begun its training at BMW’s manufacturing facility in Spartanburg, South Carolina. The machine demonstrates improved skills in grasping complex shapes, navigating obstacles, and precisely placing parts. One notable feature is its ability to self-correct errors, such as tapping misaligned parts into place with the back of its hand.
In Japan, West Japan Railway (JR West) has also introduced a new new humanoid robot for railway maintenance to tackle labor shortages and improve safety among Japan’s aging workforce. Its distinctive features include enormous arms that can be equipped with different attachments, allowing it to wield paintbrushes, chainsaws, or other tools as needed.
Meanwhile, in the United Kingdom, Shadow Home Secretary Chris Philp promotes increased automation as an alternative to relying on migrant workers. He pointed to Australia and New Zealand’s adoption of robotic fruit-picking systems and South Korea’s extensive use of manufacturing robots – noting that South Korea employs nine times more robots than the UK.
Employee response and implementation
Despite the benefits, executives admitted that introducing new technology comes with challenges.
“When we give them tech that works, we hear about it immediately. When we give them tech that doesn’t work, we hear about it very fast too,” Radhakrishnan said, describing employees’ openness with feedback.
Strategic integration
The key to successful implementation lies in gradual integration. Clark described the rollout process as bumpy but necessary. “No matter how phenomenal you are at rolling out, it’s always bad for a little bit,” he said, adding that even beneficial changes are initially met with resistance.
“Change is bad, even good change,” he remarked. The key, according to Clark, is distinguishing between early learning pains and fundamental flaws in the system.
Economic perspective
Despite common concerns about labor cost reduction, Clark points out that labor expenses are actually less significant than other operational factors such as transportation and forecasting inefficiencies.
This perspective suggests that the primary motivation for automation extends beyond simple cost-cutting measures, focusing instead on overall operational efficiency and better resource allocation.